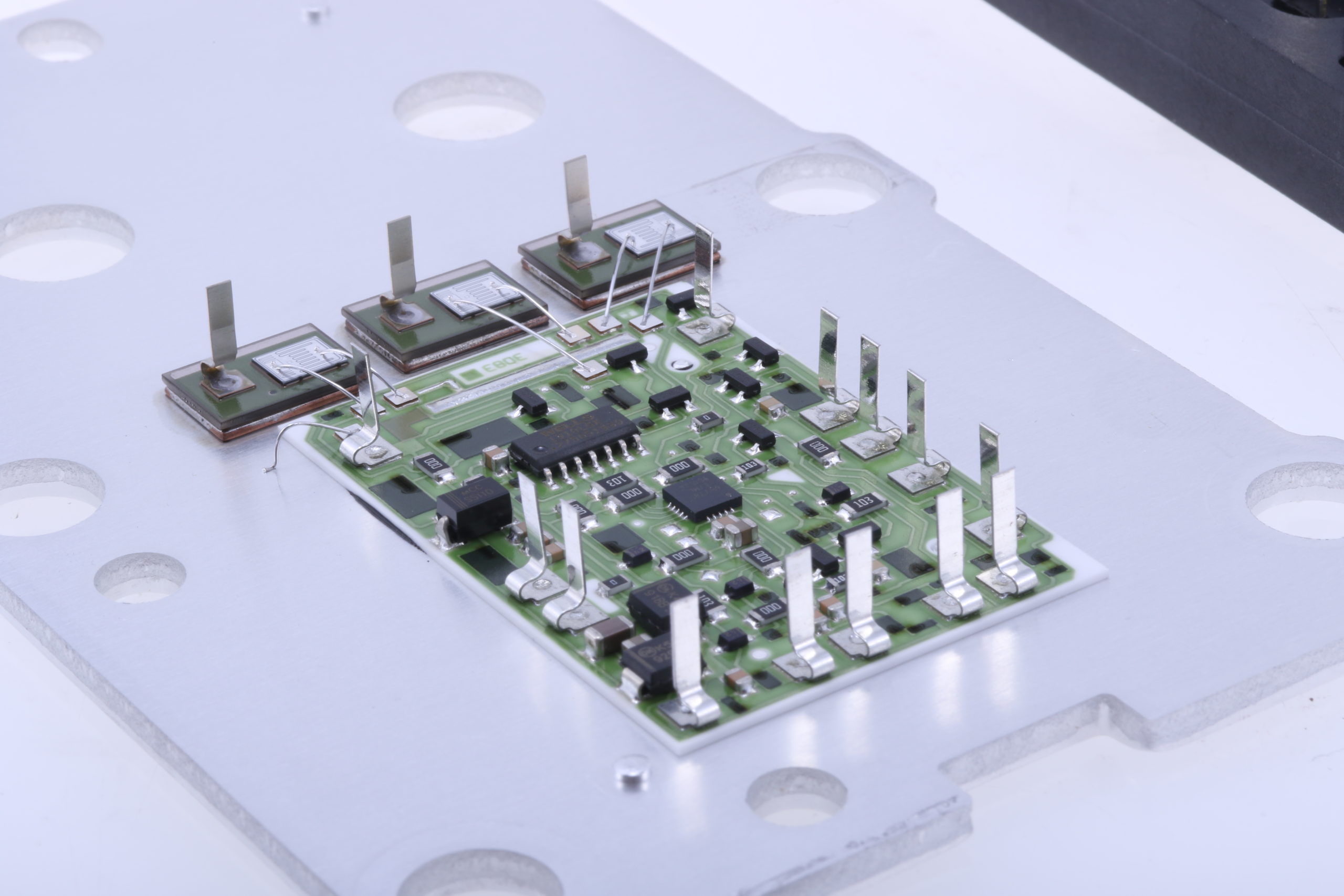
The Glass Transition Temperature (Tg) of a conventional green circuit board can be as low as 130°C. That’s a problem in power electronics applications where a combination of high component density and little space can push temperatures higher. To avoid premature failures, the answer is to adopt ceramic substrates. Here’s a look at the issue and an explanation of the advantages of ceramics.
Conventional Circuit Board Construction
The overwhelming majority of circuit boards are manufactured from FR-4. It’s an inexpensive epoxy-impregnated fiberglass material that works well in undemanding, low power applications. That’s also what makes it the first choice for many engineers when developing a new circuit. Unfortunately, FR-4 has three characteristics that limit its use in power electronics applications:
- Low coefficient of thermal conductivity
- Low coefficient of thermal expansion (CTE)
- Low Tg (generally in the range of 130 to 170°C)
Poor conductivity leads to hot spots on the board. Low CTE results in differential expansion between board and copper layers and traces, solder joints and components. And low Tg means the board can soften and distort at relatively low temperatures.
Metal structures on the FR-4 board ameliorate the issue, but they too take up space. Heat sinks and cooling fins can dissipate heat but need airflow. Plus, there’s the problem of creating a good bond between the high power components and heat sink. Eventually, it becomes clear that reliable power electronics need an alternative to the FR-4 board. That’s when it’s time to explore ceramic substrates.
Types of Ceramic Substrate
Like FR-4, ceramics make good electrical insulators. Unlike FR-4 though, ceramics can be made with thermal conductivity that rivals aluminum heat sinks.
There are many different types of ceramic but three, in particular, stand out as substrate material. These are alumina (Al2O3), aluminum nitride (AlN) and beryllium oxide (BeO). With each, traces are formed by screen printing a conductive metal paste onto the ceramic, which is then baked or fired.
Thick film ceramic PCBs use gold, silver or more often, copper, as the conductor and are baked in a nitrogen atmosphere at just under 1,000°C. (The nitrogen atmosphere prevents oxidation.) Alternative manufacturing methods are the low-temperature co-fired ceramic (LTCC) PCB process and the high-temperature co-fired ceramic (HTCC) PCB process. In LTCC the traces are usually gold while for HTCC tungsten and molybdenum are used.
As with FR-4, it is possible to create multi-layer ceramic PCBs.
Advantages of Ceramic Over FR-4
The main benefit of switching from FR-4 to ceramic PCB substrates is how ceramics handle high temperatures. The ceramic substrates identified above are notably superior conductors of heat, meaning they do a much better job of getting heat away from board devices and into the heat sinks. This also prevents the formation of local hot spots.
For comparison, conductivity values are as follows:
FR-4 0.8 – 1.1 W/m-K
Alumina 28 – 35 W/m-K
Aluminum Nitride 140 – 180 W/m-K
Beryllium Oxide 170 – 280 W/m-K
Material | Thermal Conductivity (W/m-k) |
FR-4 | 1.1 |
Alumina | 28-35 |
Aluminum Nitride | 140-180 |
Beryllium Oxide | 170-280 |
Aluminum 6061-TG | 150-170 |
A second benefit is that the CTE of ceramic substrates aligns more closely with that of the metal traces on the substrate and the components soldered to the substrate. That helps minimize stresses that can lead to component and solder joint fractures.
The bottom line is this: because ceramic substrates do a much better job of moving heat away from the sources, in power electronics applications they make a more reliable PCB substrate material than FR-4 and allow the designer to achieve higher power density designs. However, there are two other advantages to ceramics.
In high-frequency power electronics applications, FR-4 boards can suffer parasitic capacitance effects where traces and components are in close proximity. This impedes high-frequency response and is becoming a bigger issue as boards grow more densely packed. Ceramic substrate boards do not suffer this problem.
Ceramics hold up to moisture far better than FR-4. FR-4 absorbs moisture, which can be a significant concern in marine and vehicular power electronics applications. In contrast, ceramics have no such problems.
Consider Durability in High-Heat Applications
FR-4 has been the “go-to” material for circuit boards for a long time. It performs well in many applications but is challenged by high temperatures and also humidity. Many power electronics applications generate significant heat and using FR-4 substrates means risking long-term reliability. Ask for ceramic substrates and protect your devices from premature failure in high-power applications. Using ceramic substrates in high-power applications means higher reliability and smaller product footprints.