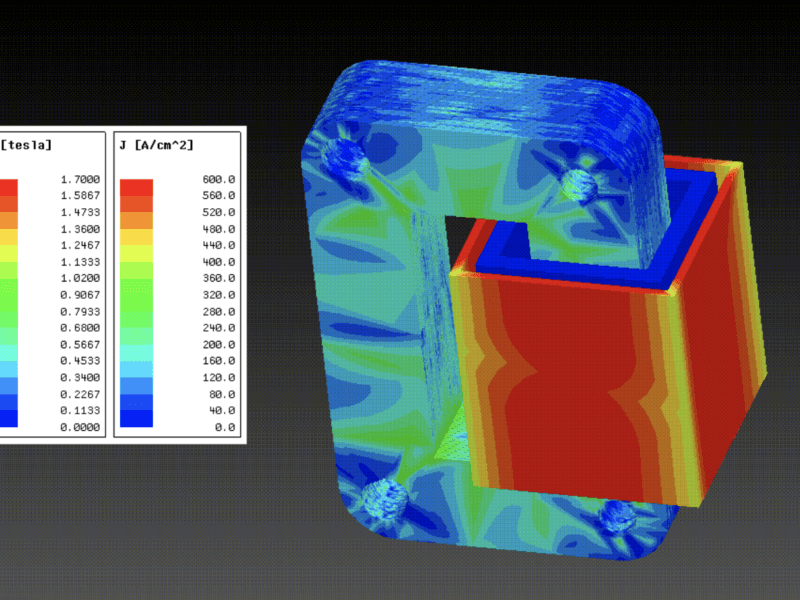
Not long ago, developing new products meant going through countless iterations of the design-prototype-test cycle. Today there’s far less physical testing, and the products developed perform better and are introduced to production much faster.
The key to this revolution is finite element analysis, or FEA for short. Wells uses the latest generation of FEA tools to develop stronger, lighter, smaller products that exceed the expectations of our customers. Here’s an introduction to FEA, how it’s used in product development, and how customers and end users benefit.
Solving Complex Math Problems
Early in the product design process engineers use Computer Aided Design, or CAD, to determine the look, shape and dimensions of the product. At Wells this could be a sensor housing, a rotary position switch or any of our many other electronic products. CAD provides an accurate 3D view of the product, but it doesn’t provide any information about how it will perform in the real world. This is where FEA comes in.
FEA lets engineers evaluate the effect of forces applied to the design. In High School physics students learn how loads cause deflection, but the examples are simplified with loads applied to a single point. In the real-world loads are spread over an area: FEA makes it possible to evaluate the effect these will have.
FEA works by breaking down each part of a product or assembly into a series of polygons linked together in a mesh. (For simplicity, think of them as tiny cubes.) Then forces are applied the polygons, which distort and pass those forces along to their neighbors, as the properties of the material permit.
Modeling how a mesh behaves involves solving partial differential equations that describe how the materials used in the design react to the applied forces. In the early days of FEA this kind of work was done by PhD-level engineers. With improvements in software tools and increasingly powerful computers, today it’s something most engineering graduates can handle.
Applications for FEA
So far FEA has been discussed in connection with modeling the stresses that result from imposing physical loads on rigid objects. This mechanical modeling is probably the biggest use, but there are many other applications. If a behavior can be represented mathematically, it can be modeled with FEA.
Another major application of FEA is modeling fluid dynamics. This is done to discover how a gas, like air, or a liquid, will pass through or around a structure. Heat flows can be modeled the same way to predict how hot or cold an assembly might get in service. (And for added sophistication, fluid flow and heat transfer could be addressed in the same model.) It’s even possible to build models of electromagnetic effects, which is of great relevance to the products developed at Wells.
Benefits of Modeling With FEA
Creating an accurate FEA model takes time, but the benefits are so extensive that it’s become standard practice for many of the products we make.
FEA reveals how a product will react and perform to whatever conditions are applied. That reduces the need to make and test physical prototypes, which saves a lot of time. Those savings are used to do more virtual testing, resulting in better performing products, while also getting products to market faster.
Models Aren’t Exact
After developing a product with FEA some physical testing is still done. This is for two reasons: it’s needed to validate the model – to prove that it’s correct – and as final confirmation that the design is fit for purpose.
Modern computer power enables the use of smaller polygons in much larger meshes, (which take longer to process,) but they remain approximations. Likewise, it’s impossible to know the exact properties of the materials used throughout the entire volume of the part or component. The textbook and manufacturer values are averages, and in addition, manufacturing processes can cause minor changes in material properties. (Work hardening of steel is an example.)
Another challenge is that some physical behaviors are very hard to model with any degree of accuracy. Friction in particular is extremely difficult.
For all these reasons, FEA models aren’t exact, and must be validated to determine if they are accurate enough to be relied upon. A good model will come within 90% of real-world performance. Should the deviations be large enough to give cause for concern, it may be necessary to rework the model to get better results.
FEA at Wells Engineered Products
Wells Engineered Products has long made extensive use of FEA in product development. In the early days this mostly involved performing stress calculations on 2D models, but as computer power and software applications have grown, so too has the range of use cases.
Today most FEA is undertaken using 3D models. Predicting stress in response to loads is still the biggest application but FEA is increasingly used for modeling fluid dynamics, heat transfer and even electromagnetic forces, (which is done by solving Maxwell’s Equations.)
The primary role of FEA is to enable better product design optimization. It does this by providing visualizations of how individual parts and complete assemblies will behave under load. That information, which would previously have been obtained through physical testing, is used to refine designs until they’re deemed ready for physical testing.
This elimination of physical testing also has the effect of compressing product development lead time. That supports customers who themselves have aggressive product development programs.
Finite Element Analysis is a Core Product Development Tool
Once seen as an interesting engineering or academic tool, FEA is now integral to the Wells product development process. It shortens lead times and results in more fully optimized designs that better meet customer and end user needs.