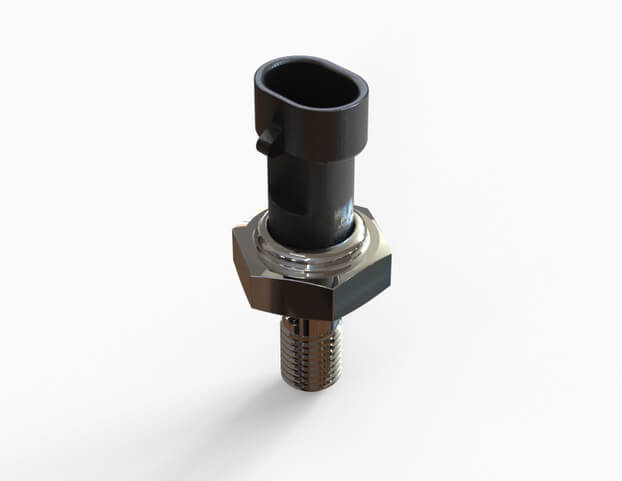
Engine lubrication systems don’t run at particularly high pressures, so when one of our customers reported that oil blasted through a prototype oil pressure sensor people were surprised, to put it mildly. Getting to the root of the problem took collaboration between Wells Engineered Products and the customer and led to a better understanding of how this particular engine performed.
Measuring Oil Pressure
Lubrication systems vary depending on engine design, but every one has an oil pressure switch or sensor. These two terms are often used interchangeably, but there is a difference. A switch checks that pressure is above a fixed threshold. If too low, it turns on a dashboard warning light, (and perhaps messages the ECU).
An oil pressure sensor is somewhat more sophisticated. Those manufactured by Wells use a piezo design that outputs a voltage proportional to the force exerted by engine oil on a piece of engineered ceramic material. This signal can be used in a binary manner but in many applications, a measurement of pressure is desired.
Oil pressure is generally proportional to engine speed: at high RPMs, the engine needs better oil flow, not just for lubrication but for cooling, too. A rule-of-thumb in the engine-building world is 10 PSI per 1,000 RPM, although this depends very much on application with some engines running lower. For oil pressure sensors, however, this means pressures are predominantly in the 30 to 50 PSI range and may occasionally go as high as 70 PSI.
Unexpected Failure
The engineers at Wells Engineered Products have a very detailed understanding of engine oil pressure sensors and a wealth of applications engineering experience. Not surprisingly then, there was much consternation when a sensor failed an early development test.
“Failed,” is something of an understatement. Somehow, oil punched a hole through the ceramic and the circuit board behind, depositing all the engine’s lubricant on the test bench and floor.
This one-of-a-kind event had the Wells team perplexed and the customer understandably concerned. The logical conclusion was that oil pressure somehow exceeded the design limits of the sensor, but in a system where the pump only delivered 60 PSI maximum, it seemed impossible.
Starting with the Obvious
Our engineering team initiated a thorough investigation to explore the high-pressure hypothesis. Identical oil pressure sensors were subjected to a high-pressure static test that exposed them to up to 1,000 PSI.
They didn’t break. Was high pressure not the problem and was something else going on? Answering that meant digging deeper into how the engine and oil pump ran.
A Collaborative Search for the Root Cause
This is where engineers from Wells and the customer came together to unearth the root cause of the failure. After an exhaustive review of the lubrication system, particularly the oil pump, exploring points such as whether the pump was lobed and sending waves through the galleries, it was decided to do instrumented testing. This would use very high sampling rates to capture transient pressure spikes.
The Verdict Was In
Tap a piece of glass with a hammer and it may not break the first time or even the second. Keep hitting it though and eventually, it will fail.
This is what was happening to the oil pressure sensor. Wells engineers were able to show the customer how their engine was delivering high-frequency oil pressure spikes far in excess of the average pressure measured previously.
The customer was surprised by this: they had not known their engine and lubrication system behaved in this manner. Once informed, they delved deeper into the cause, identifying and implementing small but important changes.
Delivering More Than Sensors
There’s an old cliché about problems being opportunities, and it was certainly true in this case. Here the opportunity was to improve oil pump performance. What’s more, the problem-solving process followed demonstrates the benefits of the collaborative approach taken by Wells Engineered Products.
In this case, Wells engineers with deep expertise in oil pressure sensors were brought together with the customer’s instrumentation and testing capabilities. Not only did this identify the cause of the sensor failure, it yielded new insights into how the engine ran, helping the customer make improvements.
Failures during development are unusual but not altogether unexpected. What matters is how they are addressed. Wells engineers believe strongly in working together with their customers to solve problems, regardless of cause or origin. It’s attitudes like these that make it rewarding to partner with Wells Engineered Products.