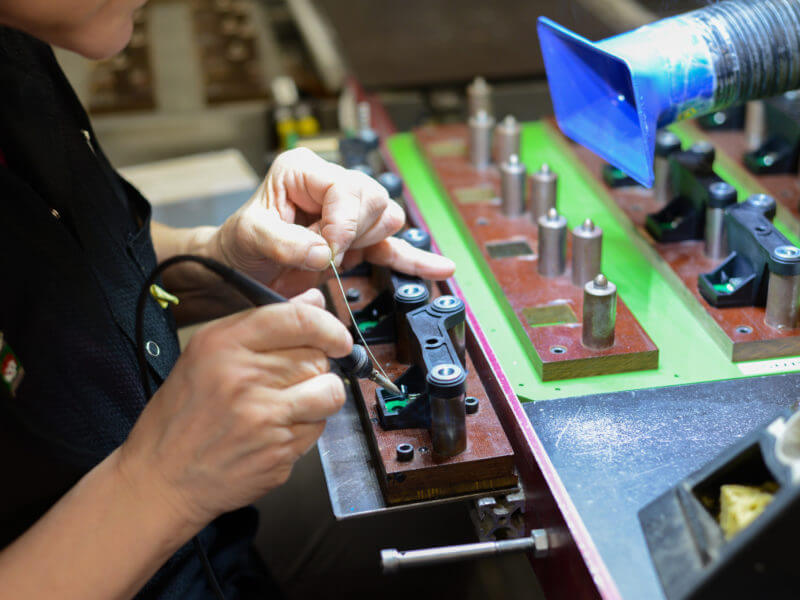
Engines are complex, customer expectations for their performance are forever on an upwards trajectory, and the regulatory environment becomes tougher each year. In a business like this, it’s essential to partner with your provider of vehicle electronic components rather than simply purchase.
The right partner helps their customer achieve their goals by delivering high-quality, reliable products exactly when needed, if not slightly before. The right partner has deep expertise in the products they design and manufacture and helps their customer solve problems and create industry-leading products that their customers seek.
The list below identifies key elements that differentiate such high-performance partners from the “me-toos.” Use it as a checklist when sourcing vehicle electronic components.
- Industry/Market Vertical Experience and Expertise
Specialization and depth of expertise are essential. A vehicle electronic components partner should be completely focused on the physics and technologies underpinning their sensors and devices. Ideally, they will have been in the industry long enough to build up the deep expertise essential for solving complex customer problems and developing innovative solutions.
- Compliance with Industry Specifications
Providers of vehicle electronics components are challenged by regulations and standards in two ways. First, as engine test regimens vary throughout the world and across industries, the chosen provider must be fully up-to-speed before development work starts. (No one wants to pay a supplier to learn on their project.)
Second, there’s no room for proprietary connections or interfaces in engine controls. Providers must be fully conversant with industry specifications like those promulgated by SAE and DOT, and design accordingly.
- Comprehensive Technology Development & Design Capabilities
Standard, off-the-shelf parts rarely deliver the best combination of performance, quality and durability. This is why a vehicle electronics components provider must have testing, validation and prototyping capabilities in addition to design.
Comprehensive testing capabilities allow a supplier to understand how the part will perform in the intended application. Validation labs, preferably certified to ISO 17025, provide the capability for methodical, disciplined testing and analysis in accordance with industry standards and best practice. Prototyping should be organized to minimize lead time with technologies like 3D printing deployed in support.
- Integrated Quality Management – Design Through Manufacturing
A formal Quality Management System (QMS) provides the framework for a disciplined and organized approach to product development and manufacturing. While many manufacturers adhere to ISO 9001 those supplying engine components and systems, especially to the automotive industry, should be certified to IATF/TS 16949.
An enhancement to ISO 9001, this places greater emphasis on scrap, returns, continuous improvement and warranty management. A company certified to TS 16949 will have in place procedures for engine-specific requirements such as APQP and PPAP as well as any Customer Specific Requirements (CSRs.)
- Manufacturing Automation
Automation isn’t just about cost reduction, even though that’s how it’s often justified. Automation reduces process variation.
First, automated machines are more repeatable and create a more consistent product. Second, implementing automation often requires manufacturers to tighten up on incoming material and component tolerances, reducing variation to ensure trouble-free feeding and avoid downtime.
Vehicle electronics components providers who’ve invested in manufacturing automation supply consistent product with minimal part-to-part variation. This prevents problems during installation, ensures reliable performance, and minimizes the risk of customer complaints.
- Volume Specialization and Flexible Capacity
In engine manufacturing, volumes span the spectrum from those built one and two at a time up to those assembled in millions per year. Further, unit quantities change during an engine’s life. Volumes start out low for prototyping and testing, increasing through production ramp-up and then declining gradually as successor engines come on stream.
Some providers of vehicle electronics components are configured for and have expertise in lower volume production. Others are set up to mass-produce millions but have little flexibility to handle demand changes effectively. The ideal provider will have capabilities and expertise to tailor manufacturing for different demand levels as needed.
- Lead Times and Responsiveness
It’s hard to think of an industry where time-to-market isn’t a critical success factor; it’s certainly true for engines, whether automotive, marine or industrial. Suppliers must be able to meet tight deadlines for prototypes, testing and product launch. This requires world-class in-house testing, certified validation labs and rapid prototyping expertise. Partnering with a supplier lacking this competence means risking late deliveries and delayed launches.
Partnering, Not Purchasing
Engine development must have been a lot easier when carburetor adjustment and ignition timing were all that mattered. Today’s engine designs, hemmed in by emissions legislation and efficiency mandates, need sophisticated vehicle electronics components to meet the demands of customers and administrators alike.
Designing, developing and manufacturing these systems and components demands highly specialized knowledge and deep expertise. This is why it’s essential to work with a partner who’s really mastered the domain knowledge needed.