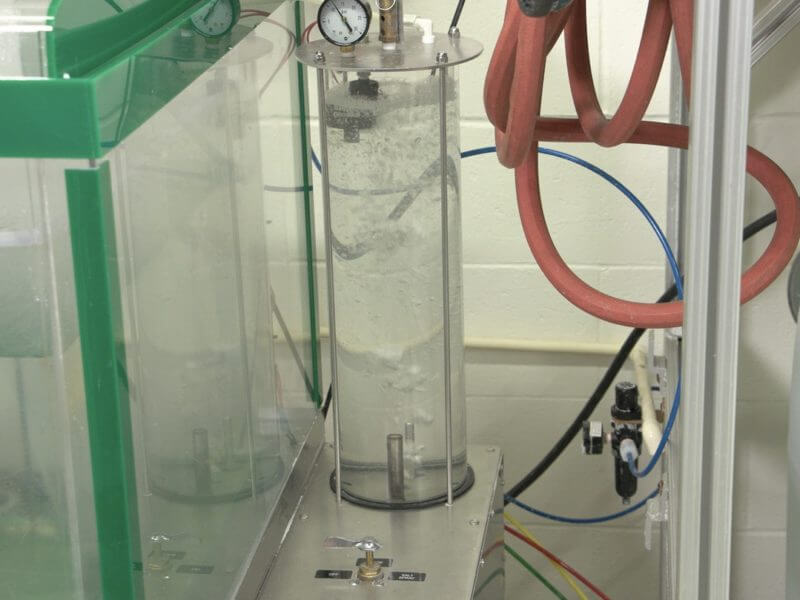
As anyone who’s dropped a cellphone in the toilet can confirm – which is about 20% of the population, according to cnet.com – water and electricity don’t get along. The moment water penetrates an electronic device circuits are shorted and delicate components die. Water killing a phone is annoying and perhaps embarrassing. When it happens to a vehicle or boat it could be life-threatening. That’s why Wells Engineered Products takes ingress testing very seriously.
Ingress testing is about verifying that water, and other potentially damaging fluids, can’t penetrate electronic packages and enclosures and damage the components inside. Here’s a dive into the importance of ingress testing, and how our engineers go about protecting devices like ignition coils, voltage regulators and sensors.
Water and More
An automated car wash can spray quite a bit of water around an engine bay but generally, unless a car or truck is driven through a creek, the electronics won’t suffer a lot of exposure to water. The same isn’t true though for motorcycles and ATVs. The electronic packages and enclosures on these are exposed to constant splashing, followed perhaps by power-washing to remove the accumulated mud.
In some locations, humidity can be an issue. Coastal areas may suffer dense fog which can condense on the surface of electronic enclosures. And as those in the Pacific Northwest will attest, some places just see a lot of rain.
Humidity causes problems in two ways. First, as the temperature changes, it’s likely to condense into liquid water. Second, high humidity can cause delamination in PCBs.
Water isn’t the only challenge electronic packages face though. Salty water, from road salt as well as ocean spray, will leave a crystalline coating that’s only too happy to corrode metal and plastic. Then there are noxious gases, especially sulfur, which are common in city traffic and again, can attack electronic components.
The bottom line is this: the electronic components on which modern vehicles depend need protection from attack by water and other fluids.
The Openings Problem
If electronic devices could be placed into hermetically enclosed packages there wouldn’t be a problem. The reality is though, these components have wires running into and out of them to provide power and transmit data. Plus, the devices themselves require assembly, which means having openings in the housings or enclosures.
Wells products protect electronics against water and other fluids in several ways. First, conformal coatings may be used to waterproof circuit boards and other devices. Then there are a range of encapsulation methods – potting and gels – that enclose the electronics and exclude water. And finally, gaskets are used to seal openings like those required by wire harnesses and enclosure covers.
Not every electronic device needs wire harnesses: in principle, it’s sometimes possible to connect wiring to studs or terminals extending out through the encapsulation. However, Wells engineers have learned, partly as a result of ingress testing, that such an approach is not particularly waterproof or durable. The alternative, designing with integrated sealed connectors, is more easily protected, and to a higher level.
Ingress Protection
Engineers will be familiar with the levels of Ingress Protection (IP). Products are often advertised as having IP 65, 66, 67 or 69 protection. These IP numbers have formal definitions in the CENELEC EN 60529 standard. (In the US, NEMA provides a similar system for classifying levels of ingress protection.)
In this scheme, the first digit indicates the size of a solid object against which ingress protection is provided. A 2 means fingers can’t reach inside. A 6 indicates that an enclosure is dust-tight.
The second digit relates to protection against liquids. A 5 means that the package resists penetration by water sprayed at 4.4 psi from a distance of 9.8’. Moving up to 6 means increased protection against jets of water, while 7 indicates that a package will not allow water in while submerged for 30 minutes. Thus, electronics inside an enclosure rated to IP67 will continue to function even after a brief period of complete immersion.
Verifying the level of protection a package or enclosure provides is determined by testing.
Ingress Testing Performed by Wells Engineered Products
The three main types of ingress testing performed by Wells include:
- Salt Spray
- Submersion
- Humidity
Each test is performed according to strict procedures that ensure consistency and repeatability. EN 60529 or other procedures are followed where appropriate, but Wells engineers will also perform test regimens specified by customers.
Where additional, less common testing is needed, Wells has a network of test partners who will undertake this work. Verifying protection against noxious gases is a prime example.
Ensuring Product Reliability
Water is fatal to electrical systems and delicate electronics, so these devices must be placed into enclosures sealed against ingress. Likewise, salt, sulfur and other noxious gases can attack and corrode electronic packages.
Verifying the effectiveness of the protective measures taken requires ingress testing. We have the resources and expertise necessary to perform ingress testing to customer and international standards. This ensures the ignition coils, sensors, voltage regulators and other electronic products manufactured by Wells will perform reliably in the most arduous conditions.