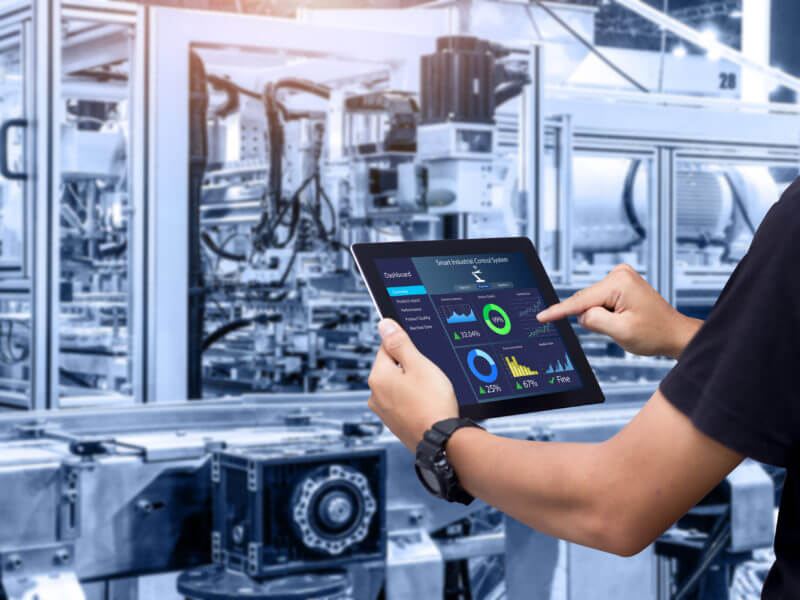
Automated manufacturing is the norm at Wells Engineered Products. Visitors touring the production areas see robots and automated machinery forming, joining, bonding, assembling and packing the complex electronic and electro-mechanical devices made there. Increasingly though, the team at Wells is thinking about what comes next.
At Wells, this next step is called, “intelligent manufacturing” and implementation is already underway. Here’s what it means and what it delivers.
Reasons For Automating
Automation benefits manufacturers like Wells in many ways. By moving workers from hands-on manufacturing processes to overseeing machines that do the physical work, automation improves safety and quality while cutting costs. More specifically:
- People are no longer loading and unloading
- Eyes aren’t at risk of flying objects or debris
- Hearing is protected because machines are enclosed
- Fume extraction from enclosures means no one breathes unhealthy vapors.
- Automated processes are more consistent
- Robots and automated machines don’t get tired or distracted
- Automation applies the same forces on every cycle
- Robots follow the same path every time
- Output rises and costs fall because machines don’t need breaks or vacations
Limitations of Automation
Automated manufacturing equipment is by necessity very complex, and this creates challenges. First, some automated equipment needs a lot of adjustment to change over between products. (Others, like robots and CNC machine tools, need only a change of program.) Changeovers are becoming more frequent as customer requirements for increased customization lead to shorter production runs, and this eats into capacity.
Second, automated equipment can make bad parts as quickly as it makes good. When no one is watching over each process there’s a risk that changes in a component or material, tool breakage or failure of a machine part can result in a large pile of nonconforming product.
Complex equipment also has more that can go wrong. While individual rods, motors and sensors are reliable, put them together in a sophisticated machine and there’s a greater need for maintenance to keep everything working as it should.
Taking a Proactive Approach
When things go wrong with automation, most manufacturers shut down the equipment and start troubleshooting and problem-solving. The intelligent manufacturing philosophy that Wells is adopting provides an alternative: Rather than react to problems, intelligent manufacturing means gathering data and using it to avoid problems.
On the factory floor, the two key elements of intelligent manufacturing are advanced sensors and data capture and analysis tools.
Advanced sensors measure parameters like distance, speed, temperature and pressure in real-time, and also communicate their findings. Some even have on-board analysis and trend monitoring so they need only report exceptions.
Vision systems are a type of advanced sensor. Cameras take pictures of every part being made and these are analyzed by software that verifies components are present, checks dimensions and looks for flaws.
In some cases, these measurements are used to adjust the manufacturing processes automatically and in real-time. This lets the equipment accommodate small variations in the dimensions and properties of components, which would otherwise stop production or affect quality.
In-line testing is another application of data collection to improve manufacturing efficiency and product quality. Automated equipment can perform tests at line speeds and transfer the data for trend monitoring, analysis and traceability.
Data is only of value when it’s put to good use, and that’s the second part of the intelligent manufacturing approach. Data provides insights into problems, both those that have occurred and those that might happen. According to Forbes, the more you can automate and deliver data-driven reports, the faster people are going to be able to understand the problem that needs to be solved.
Intelligence Upstream and Downstream
At Wells, we’re extending our intelligent manufacturing philosophy back through the supply chain and forward into the warehouse and distribution system. Supply chain modeling is an example, used for demand forecasting and inventory optimization.
Electronic components like MOSFETs and ASICs can go “end-of-life” quickly with implications for the products Wells ships: a proactive approach means monitoring for such announcements and working with customers on alternatives.
Our products are sold and shipped in both very high and very low volumes. To meet these demands, packaging, warehousing and shipping have implemented systems that provide the flexibility to pick and dispatch one part or 100,000 as needed. In this case, intelligence supports flexibility and lets us anticipate customer needs so as to provide excellent service.
Benefits For Wells and the Customers
Intelligent manufacturing delivers many benefits. Monitoring and adapting to trends results in less product variability. Customers benefit from more predictable performance and higher accuracy and reliability while Wells gains from higher material and part yields and fewer production stoppages.
Machine and process data supports predictive maintenance. Rather than planning routine maintenance that may or may not be needed, this is where work is scheduled in response to indications of changes in machine condition. For example, if data indicates bearings last 100,000 cycles, replacement will be scheduled at 80,000. This reduces unplanned stoppages which makes production both more efficient and more stable and predictable.
These improvements reduce waste, which benefits everybody. They also improve Overall Equipment Effectiveness (OEE), which is one of the key measures of machine utilization. OEE matters because it relates to capacity: higher OEE means more part-making capacity on Wells’ production lines. It also increases overhead dilution, which again benefits customers and Wells alike.
Intelligent Manufacturing is a Work-in-Progress
Advanced sensors have turned what was a trickle of data on manufacturing to a veritable river. As sensor usage continues to grow that river will become a torrent. Our manufacturing leadership team is looking at how we will handle and benefit from all that data, and one answer is artificial intelligence (AI).
AI has many uses in manufacturing, but a major application is in spotting trends and exceptions to trends. AI is starting to be deployed in part inspection, in testing, in maintenance, warehousing and scheduling. Quite soon there will probably be no part of manufacturing that isn’t using AI to improve quality and efficiency, as it’s the logical next step after manufacturing automation.